工場での生産現場では、さまざまなトラブルが発生することがあります。
これらのトラブルは、業務効率の低下や製品の品質に悪影響を及ぼす可能性が高いため、迅速かつ的確な対処が求められます。
本記事では、工場で起こりやすいトラブルの原因を明確にし、その解決法を詳しく解説します。
工場でのトラブル対策を行うことで、生産性向上と品質向上を目指しましょう。
1. 人的ミスによるトラブル
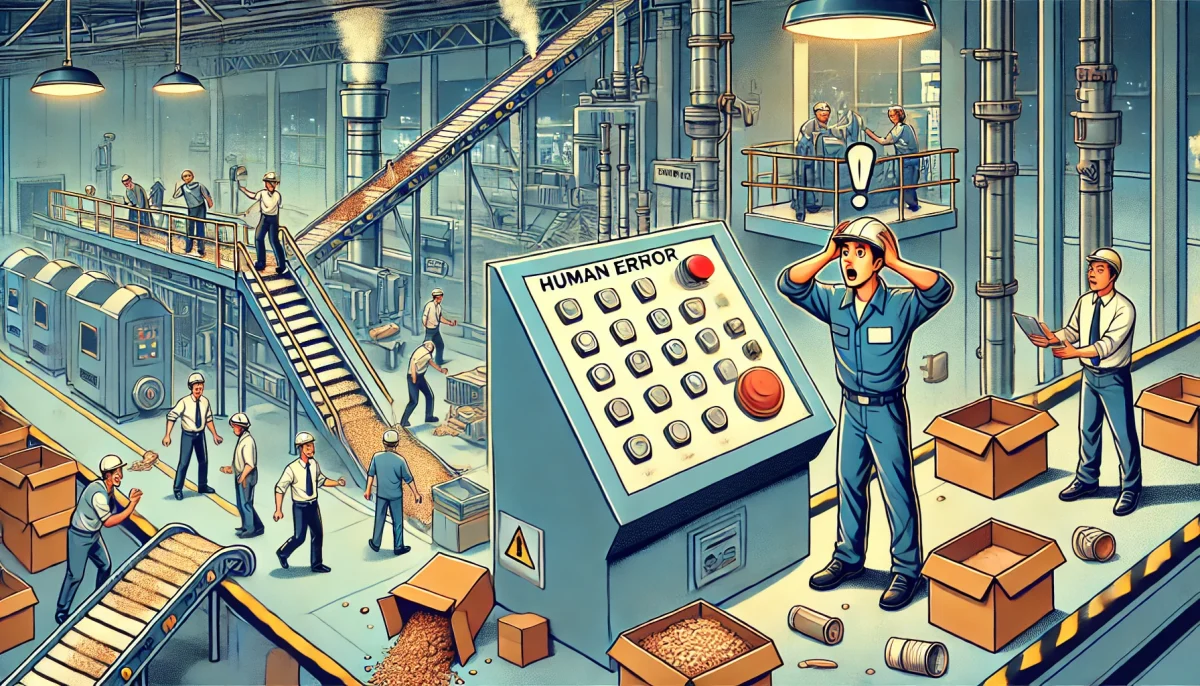
作業手順のミスが引き起こすトラブル
工場では、正確な作業手順に従うことが非常に重要です。
しかし、複雑な手順や時間に追われる状況では、作業者が手順を飛ばしたり、間違った方法で作業を行ってしまうことがあります。
このような人的ミスは、品質不良や機械の故障など、深刻なトラブルにつながることがあります。
解決法:作業手順の見直しと標準化
作業手順を定期的に見直し、誰でも分かりやすい標準作業手順書(SOP)を作成することが重要です。
さらに、新人研修や定期的なトレーニングを行い、全員が適切に手順を理解し実行できる環境を整えましょう。
コミュニケーション不足によるトラブル
工場内のチーム間、またはシフト間でのコミュニケーションが不足している場合、作業がスムーズに進まないことがあります。
情報伝達がうまくいかないと、作業内容の重複や、必要な作業が抜け落ちる可能性が高まります。
これにより、生産ラインが止まる原因にもなりかねません。
解決法:情報共有の仕組みを導入
定期的なミーティングや、報告書を共有するためのシステムを導入し、情報の一元管理を徹底しましょう。
例えば、デジタルツールを活用して、リアルタイムで情報が共有できる仕組みを導入すると、コミュニケーションの質が向上します。
不慣れな作業者によるトラブル
経験の浅い作業者が、十分な指導を受けずに難しい作業を担当すると、ミスやトラブルが発生しやすくなります。
これは特に繁忙期やスタッフの入れ替わりが激しい時期に多く見られます。
解決法:現場の監督体制の強化
新人が作業を行う際には、経験豊富なスタッフがサポートし、問題が発生した際にすぐ対応できる体制を整えましょう。
現場監督者を増やしたり、問題発生時にすぐ報告できる仕組みを作ることも有効です。
2. 機械トラブル
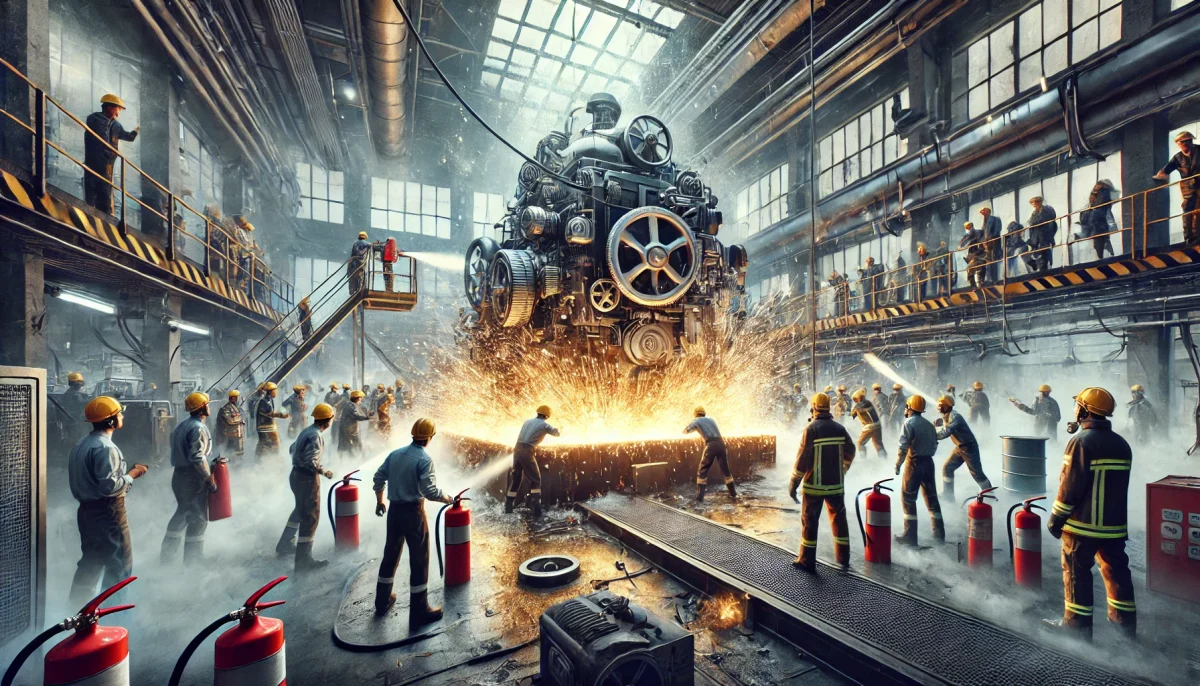
機械の老朽化によるトラブル
工場で使用される機械は、定期的にメンテナンスを行わなければ、老朽化が進み、故障のリスクが高まります。
古い機械はパフォーマンスが低下し、生産効率に影響を与えることが多いため、これを無視すると大きな損失につながります。
解決法:定期的な点検とメンテナンス
機械の定期点検とメンテナンスを徹底することで、老朽化によるトラブルを未然に防ぐことができます。
また、一定の使用期間を過ぎた機械は、故障前に更新することも重要です。
突発的な故障によるトラブル
機械は予期せぬタイミングで故障することがあります。
これが生産ライン上で発生すると、大幅な遅延が生じるだけでなく、場合によってはライン全体が停止することもあります。
解決法:予防保全の導入
突発的な故障を防ぐために、機械の状態を常に監視し、異常が見られた場合に早期に対応できる「予防保全」を取り入れましょう。
IoT技術を活用して、機械の稼働データをリアルタイムで監視するシステムを導入するのも効果的です。
操作ミスによる機械トラブル
機械の操作が誤って行われると、機械に負荷がかかり故障する原因となります。
特に新しい設備を導入した際に、このような操作ミスが増えることがあります。
解決法:操作研修とマニュアルの充実
新しい機械や技術が導入された際には、全ての作業者が操作方法をしっかり学べる研修を実施することが必要です。
また、わかりやすい操作マニュアルを作成し、常に現場で確認できるようにしましょう。
3. 供給チェーンの問題
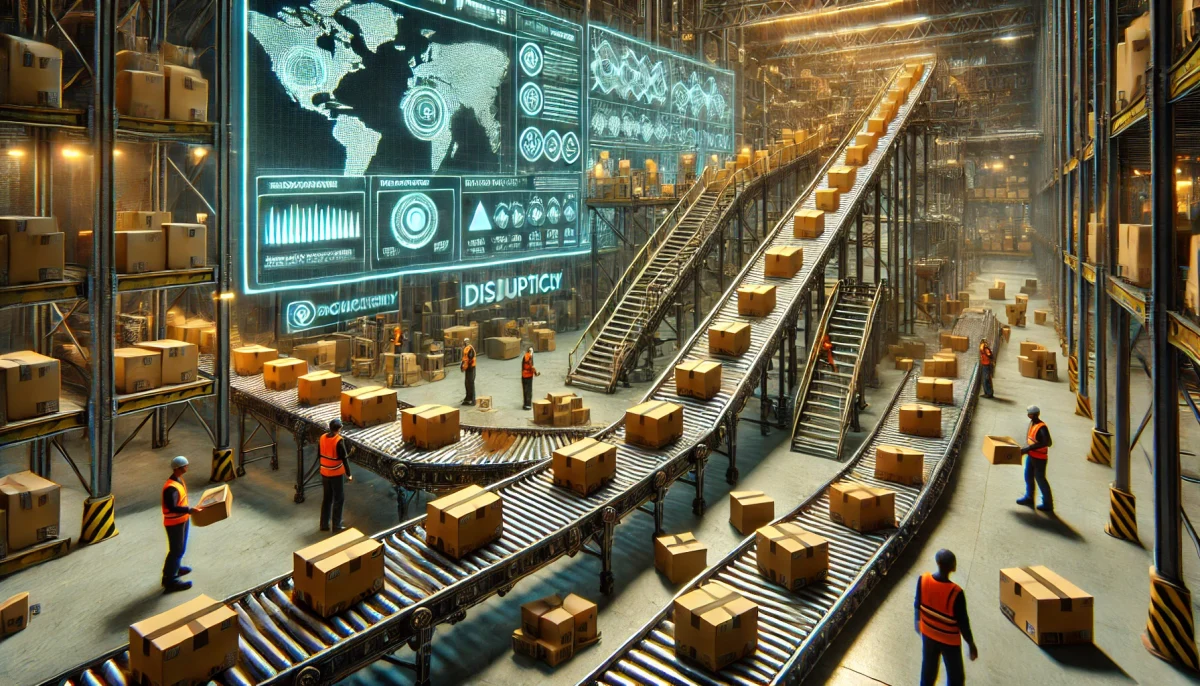
原材料不足による生産ストップ
工場で必要な原材料の供給が滞ると、計画通りの生産が行えず、生産ラインが止まってしまうことがあります。
特に外部のサプライヤーに依存している場合、サプライヤー側のトラブルも影響します。
解決法:複数の供給ルートを確保
原材料の供給元を複数確保することで、1つのサプライヤーに依存するリスクを分散させることができます。
また、在庫管理を徹底し、予備の材料を確保しておくことで、緊急時にも対応可能な体制を整えましょう。
サプライチェーンの遅延によるトラブル
物流や輸送の遅延は、供給チェーン全体に影響を与える可能性があります。
例えば、天候や交通状況による影響で、納期が遅れ、生産に必要な部品が揃わないことがあります。
解決法:納期の余裕を持たせた計画
輸送に関わるリスクを考慮し、納期に余裕を持った計画を立てることが重要です。
また、サプライヤーと密に連絡を取り、遅延が発生した場合には迅速に対応できる体制を整えておくことも大切です。
品質不良な材料の納品によるトラブル
サプライヤーから納品された材料が品質基準を満たしていない場合、製品の品質に影響を与える可能性があります。
このようなトラブルが続くと、最終製品のクレームにもつながりかねません。
解決法:品質管理体制の強化
材料の品質を確保するために、サプライヤーとの契約に品質基準を明確に記載することが大切です。
また、納品時には必ず材料の検品を行い、基準を満たしていない場合はすぐに対応できる仕組みを導入しましょう。
まとめ
工場でのトラブルには、人的ミス、機械の故障、供給チェーンの問題など、さまざまな要因が関与しています。
それぞれのトラブルに対して適切な解決策を講じることで、生産効率を高め、品質の向上を図ることが可能です。
特に、作業手順の見直しやコミュニケーションの改善、定期的な機械のメンテナンス、予防保全の導入などを取り入れることで、トラブルの発生を最小限に抑えることができます。
今後の工場運営において、これらの対策を活用し、トラブルのないスムーズな生産環境を築いていきましょう。